
Viking Hammers Forged Like Axes?
On January 30, 2015 by jaustinLast year I came across a couple of images on the internet which showed tools recovered from the graves of Viking blacksmiths. In both cases there were hammers of a particular, one-sided design which nowadays is associated with blade smithing. When I saw the first picture, which Matt Stagmer posted to Facebook from the book

Experimenting with Axe Socket Forging
On January 11, 2015 by jaustinOne of my longest standing goals as a professional blacksmith has been to forge socketed wood working axes in the traditions of northern European examples. In my opinion these axes are quite possibly the most beautiful tools in the world. The forge welding in these axes is complex and requires a strategy, tool-set and control
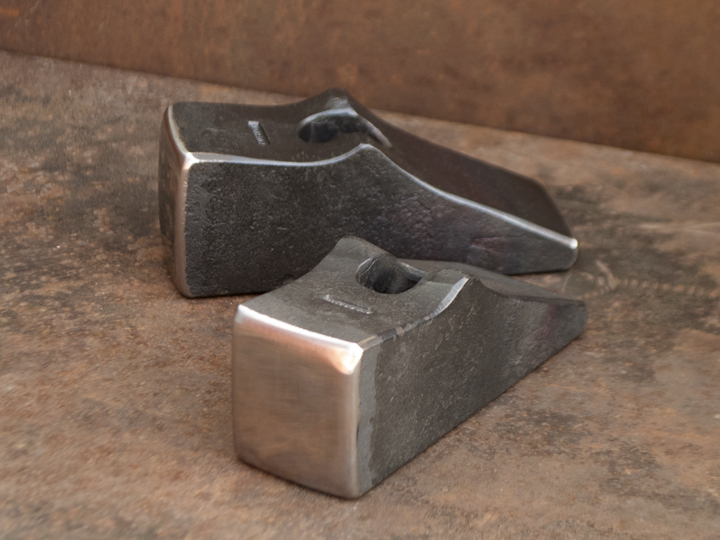
New 3lb. Viking Style Hammers (Forge Welded)
On October 23, 2014 by jaustinTwo new 3 lb. Viking style hammers are on their way to customers today. One is going to a blacksmith in France and the other to a friend just north of me here in California. Both have low-carbon steel bodies forge welded to high-carbon faces and peens. The process is very time consuming but it

A New Pair of Axes
On September 26, 2014 by jaustinThis pair of axes is ready to go to a good customer in the South East. He asked for a somewhat “matched” set to mount together so I picked out 2 pieces of similar size and heft which complimented each other from a small batch of axes I was working on. He wanted a finish

New DVD Tutorial Now (finally) Available!
On September 6, 2014 by jaustinAt long last the DVD Tutorial entitled “Forging a Viking-Age Broad Axe / Traditional Asymmetric Wrap” is finished and ready to ship! A joint project with film maker Anna Geyer, this DVD has been over a year in the making. It is 62 minutes long, professionally produced, and covers in great detail the process of