
Swedish Carpenter Axe: Fixing a Poll for Forge Welding
On March 22, 2020 by jaustinI’ve let this website lay dormant for almost 2 years now while time has flown by in my shop – much of it spent on non-axe related work. But that doesn’t mean that I’ve neglected axe forging – actually far from it. I have forged a number of larger Norwegian style hewing axes that I
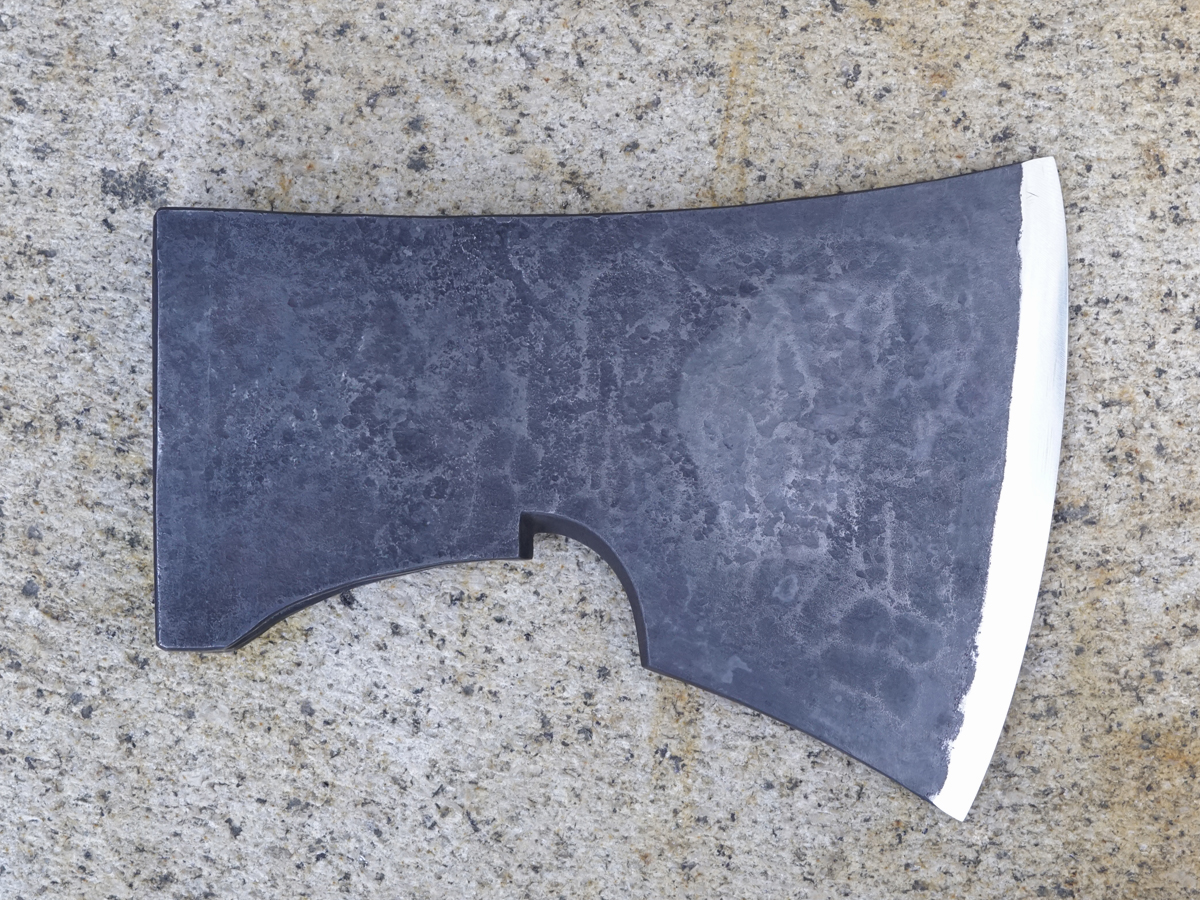
Forging Study: 5″ Norwegian Carpenter Axe
On May 15, 2018 by jaustinOn my most recent trip to Norway in May, 2017 I got to meet with the eminent traditional house builder and author Henning Olstad. Besides visiting his beautiful farm I had the opportunity to study several of the axes that he uses everyday to build houses in the many traditions of Norway. One commonly used

Axes for Sale
On February 16, 2017 by jaustinIn 2016 I traveled to 3 places to teach or demonstrate traditional axe forging. They were: Ferndale, California (Spring Conference / California Blacksmith Association), Peters Valley, New Jersey (the PV school of crafts) and Salt Lake City, Utah (ABANA Conference). In each case I brushed up on my skills in the weeks leading up to

Making Viking Age Tool Steel
On December 16, 2016 by jaustinThis year I will be teaching a class on the making and use of a common type of tool steel which was forged into tools and weapons in the Viking era. It is now often called “Shear Steel” to denote its high quality, i.e., suitable for demanding use in the blades of shears. The process

My First Go at a Horned Anvil in the Viking Style
On August 19, 2016 by jaustinOver the last couple of weeks I put some of my free time into forging a small, horned anvil with my friend Jonathan. I chose a simple form reminiscent of some of the horned anvils of the Viking era – basically a squarish anvil with a tapered base and a small, flush horn off of